These are the pieces I ended up with I turned the end of the main barrel to 25mm for my collet chuck, I made a useless indexed collar for the adjusting screw, poor design, the gib dowel I detented so the grub screws would hold this in place while the tool holder moved out, a piece of toll steel I ground to
the middle and put a cutting edge on it, the small bar with 3 hole fits on the tool holder by the small holes and is move forward by the adjusting screw going through the larger hole which is threaded m6.
I recess the other side of the main body, really badly, for the adjusting screw, drilled and tapped the tool holder to hold the square tool in a round hole.
Here you can see the basic idea the 2 grub screws bear down on the 6mm gib rod, it only needed 1,I was surprised how hard this clamped down.
Between the main body and the small plate on the tool holder is a small spring which keeps the tool holder in, loosening the grub screws on the mail barrel
and a turn on the adjusting screw brings out the tool holder, to be honest the whole assembly looks gruesome. I was not convince this was going to work and I had a mornings work would have to be re-done in making some thing else, or worse buying something Ug!!
But the result, for me was a surprise, I would not have believed it, after a few passes I started to mess with speeds and feed rates then got bored with turning the handle and wrote a program to control the Z axis it took a while cus I was boring both plates at the same time, I had to adjust the head after every cut,
when I got close to size, because I have no way of measuring the size of the bore but a vernier I had to move the work from under the cutter try the barrel move the work back under the cutter, cut again move the work, etc,etc, till the barrel fitted lovely,
Next step!!!! not sure might have a beer
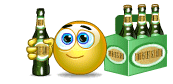