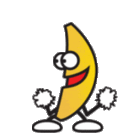
The blown mill Motor PC board arrived today and it is installed and it's a mill again.
All it took was cubic money. About $317.
Grizzly made it easy. All the wires were marked clearly with tags. Two plugs and about 6 wires got it done.
This is the offending PC board.
View attachment 232867
These are the offending components. The two on the right are melted and burnt.
View attachment 232868
I have no idea what they are, but replacing them would require major surgery. They are soldered in (8 pins each) and the only way to get to the back of the board would be to unsolder 24 large pins from the board that are attached to gizmos that are screwed to the heat sink on the back of the board. That would be to just get access to the 24 pins that attach the burnt components. Screws hold the other gizmos on the heat sink that can't be reached unless the pins on the gizmos are unsoldered. There is about a half inch between the bottom of the board and the heads of the phillips screw heads.
It might be possible to clip the component pins from the board and splice the new component pins to the stubs, but that would be some tricky close quarter solder work.