T
TOOLMASTER
Forum Guest
Register Today
this is how. 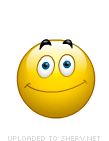
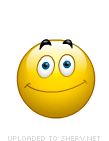
I agree, the sound is important. I don't understand how someone can enjoy riding a vehicle that can be heard 10 mins before it arrives.
I just love the whole design john, never thought of doing a muffler that can be opened up. I bet you could fine tune the noise by placing a baffle between the inlet, and outlet tubes, with the size adjusted for sound.