- Joined
- Nov 25, 2015
- Messages
- 8,389
I used the Hobart stuff to make my follow rest. I did bevel it as I wanted a flat joint. The only danger is heating the base metal too much. Even using mapp, it's easy to do. I got the rods to fix a garage sale band saw that had a gear box on it. The damn thing had so many cracks......
Anway, the brazes came out great. last pick in #13, and 14
www.hobby-machinist.com
Anway, the brazes came out great. last pick in #13, and 14
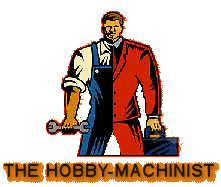
South Bend Lathe 9 Need an opinion of drilling the carriage for a left side follow rest.
That works well, but you can also just turn the QC tool holder around so that one of the dovetails face to the right to mount the tool right under the FR jaw or very near to it, this does make the locking handle sit in an inconvenient location, but I just remove it temporarily. well, since I...
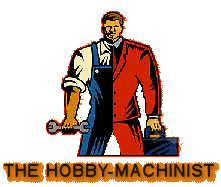