- Joined
- Jan 2, 2019
- Messages
- 7,296
It should also be pointed out that some things, like squaring up material, which one might think are only possible on a mill can be easily accomplished on a lathe with a 4 jaw chuck.Sigh.
"Blunt".
So much for "The Friendly Machinist Forum!"
I'll be sure not to ask stupid questions in the future. No sense risking "blunt" answers.
Lecture over.
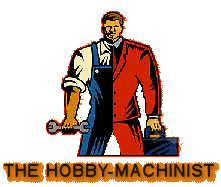
Hilco Model 2
I bought this little universal cutter grinder and can't find anything about it on the interwebs. Motor is a Dumore Type 2GM which I also can't locate. The machine is pretty simple so I don't think I really need any manuals or the like but it would be nice to know a little history. Hilco...
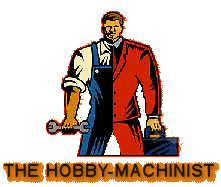
From round stock on my 100 year-old Seneca Falls Star.
If you want to see the lengths some of us have gone to when in your situation.
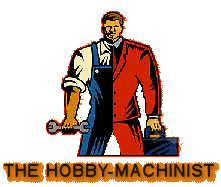
Cheap Acme Threads for Cheap X-Y Table
Hi, I'm trying to improve a Chinese X-Y table and was looking for a way to reduce backlash. Just wondering if anyone has done something like this guy does in his video? If so, what kind of plastic would you use, I have a suitable piece of delrin that might work if the properties are right...
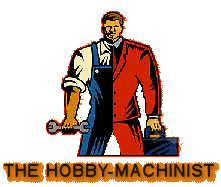
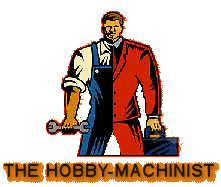
Homemade vertical mill/drill CNC project
I'm sure some of you have seen my posts in the general section about this project. https://www.hobby-machinist.com/threads/homemade-vertical-mill-drill.77611/page-3#post-664686 But now that I'm ready to start on the controls I figured it would fit better here (mods please let me know if...
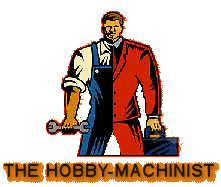
We’re all routing for you but much like when someone says they’re getting a great deal on a new lathe on eBay we’ve seen how this plays out.
If you haven’t already get very familiar with your lathe and all the different operations that can be done with it.
Reach out in the mentors section and see if you can find someone local who’s shop you can visit in person.
Keep searching on here for information on your project, you’ll find plenty.
And most important, pictures. We need pictures

John