Hello everyone,
I thought I would let you all know that I have had some some time to reflect on things.
Scraping is good and fun, however it is hard work. When a hobbyist undertakes scraping it is usually because grinding is so expensive or difficult. In my case, after starting and progressing with the machine, I have found that I would need to shift too much material. Having spoken to a number of people in the trade, the consensus seems to be "Buy a new one". The quotations for the bare minimum of grinding all seem to be around the same price as a new machine.
Now, considering that I want to convert the barsteward to cnc, and have already got all the goods I was faced with 3 options.
1) Bite the bullet: Grind and apply turcite (£2200)
2) Keep scraping and apply turcite (4 months of evenings, figure out how to fix the dovetails, make a dovetail prism etc etc....)
3) Mill the bugger to within scraping range, scrape it flat/parallel/square and apply linear rails ( 1 month of evening, £600 in rails, £100 in extra materials to increase the travels).
As you may have guessed, the last option is the one I am going for.
I have access to machine tools and a biax so as long as the machine tools can get me close, and I have 90deg angles, I can proceed with good speed. Added benefit is the elimination of any set warpage that came with the machine.
So today I have started eliminating the dove tails on the base. The datum faces will be the front of the base and the clearace plane that I have scraped flat to 20dpi already.
Here I am zeroing on the front face. I guess I could have clocked on the dovetail but knowing how out they are I would just be wasting mu time cranking the wheels. Only one clamp to get a pivot point. The base must weigh around 90kg with the extra ballast I put in it a while ago (epoxy sand and gravel)
The milling machine I am currently using is my old trusty RF30 which give a surprisingly good accuracy when I make sure I account for slop/inaccuracy in the ways.
This is where I got to before curfew:
A preliminary model of what I am going to achieve
.
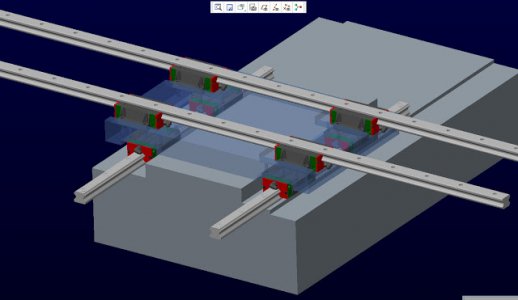
And before anybody says anything, the y-rails will be supported before I am done.
So the project is now a " Make a cheepo mill, into a machining centre" pigs ear to purse, Cinderella story.
Will keep updating as I go ahead.
Question for Richard, (as usual) since he has taught the Taiwanese to do exactly this: is 5DPI good enough or should I try and get 20-30dpi for the rail mounting surfaces?
Regards
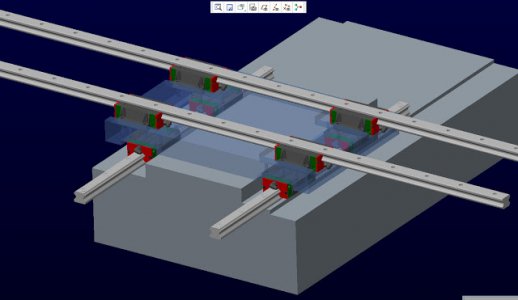