- Joined
- Feb 8, 2014
- Messages
- 11,176
It's done.
\
Adhering to the hobby machinist creed, why buy it when you can make it at 10 times the cost?
Pretty sure this part is available from Acer for a couple hundred bucks, but what fun is that?
Turning a hundred bucks worth of aluminum into a pile of chips is just too much fun.
OK, the final operations. I flipped it over and took a light skin pass on the top just to flatten it out, then pocketing the face 0.201 deep. This will leave 0.150 for the face thickness. 3/8 solid carbide, 2 flute end mill. 3000 RPM, 10 IPM, .125 DOC, and a 40% stepover.

The final pocket pass, about 61 minutes run time.

And the pocketing is finished, including the tach and switch mount holes. Same end mill and conditions as above. I again proved that the sign is important in entering the work height, the switch and tach pockets start at -0.201 in the Z axis, I entered 0.201 which means that it took three air passes before it started cutting metal.
Not very efficient, but the run time per pass was reasonably short and I'm not in that big of a hurry. If I had to make another one I would fix that.

And the final operation; rounding over the edges. For this I'm using a Harbor Freight, 0.062 radius, carbide router bit. 0.031 DOC per pass, 3000 RPM, 10 IPM. I modify the bearing type router bits by removing the bearing then mill off the bearing stud so it will cut flush. Don't get to greedy with the cut using a 1/4 shank router bit in a mill and keep it chucked up as short as possible..

The nearly finished part, ready for deburr and a little filing in the tach hole to remove the corner radius so the tach will go in the hole.

And ready for installation...

Don't have the M6 cap screws yet, Guess I'll just have to hold it in place..

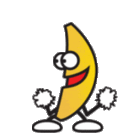
Adhering to the hobby machinist creed, why buy it when you can make it at 10 times the cost?


OK, the final operations. I flipped it over and took a light skin pass on the top just to flatten it out, then pocketing the face 0.201 deep. This will leave 0.150 for the face thickness. 3/8 solid carbide, 2 flute end mill. 3000 RPM, 10 IPM, .125 DOC, and a 40% stepover.

The final pocket pass, about 61 minutes run time.

And the pocketing is finished, including the tach and switch mount holes. Same end mill and conditions as above. I again proved that the sign is important in entering the work height, the switch and tach pockets start at -0.201 in the Z axis, I entered 0.201 which means that it took three air passes before it started cutting metal.

And the final operation; rounding over the edges. For this I'm using a Harbor Freight, 0.062 radius, carbide router bit. 0.031 DOC per pass, 3000 RPM, 10 IPM. I modify the bearing type router bits by removing the bearing then mill off the bearing stud so it will cut flush. Don't get to greedy with the cut using a 1/4 shank router bit in a mill and keep it chucked up as short as possible..


The nearly finished part, ready for deburr and a little filing in the tach hole to remove the corner radius so the tach will go in the hole.

And ready for installation...

Don't have the M6 cap screws yet, Guess I'll just have to hold it in place..

Last edited: