- Joined
- Feb 2, 2014
- Messages
- 1,208
The mower is mounted on my 1951 Allis Chalmers tractor and is just under 8 feet wide.
Here is the thread.
www.hobby-machinist.com
I will be working on both projects at the same time.
Ray
Here is the thread.
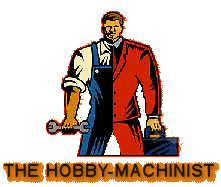
Building a New Mower
I made a mower for my 1951 WD Allis Chalmers Tractor in 2006 and over the years I have made some improvements and repairs but I knew the mower was getting kind of weak in the knees. I thought I should have a closer look and thought I would just need to do some minor repairs to the frame and be...
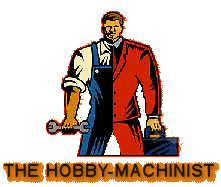
I will be working on both projects at the same time.
Ray