Here is a short rant, Stop using a hammer to take apart these machines
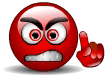
, I was looking around on you tube for some direction on taking apart the headstock and got a little sick after watching them.
I was inspired by one video though and here is the resultant solution and the steps I took to disassemble the head stock:
Remove rear take-up nut and spindle gear.
Remove woodruff key
Remove screws from bearing cap
Loosen set screw on bull gear.
Attach shop made fixture to pull spindle.
Right side of tail stock, note the jack screw/stand offs are use to give enough travel for the bearing holder to release from the head stock casting.
Left side of tails stock.
Installed spacers between hub on bull gear and head stock casting to prevent applying pressure to the outer edge of the bull gear. (Trivia question can you tell what I used for spacers.)
Tighten the nut and look at that the tail stock and bearing assembly pops out, no hammer required to remove it.
Here are the parts of the puller I pieced together
36" 1/2" all thread rod
3 1/2" nuts
2 1/2" flat washers
1 2" flat washer (I think) it need to be larger than the spindle
2 7/16" x 6" lag bolts (used as jack screws/stand offs)
2 7/16" flat washers
2 7/16" nuts
I hope this helps someone and hopefully it will make Mr. Pete happy, no hammer and chisel mechanic here.
