- Joined
- Dec 26, 2015
- Messages
- 2,079
I wrote that doc just for you.
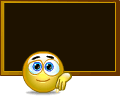
Power feed on the Y and powered head positioning are what drove me to the 935 (I put power feed on the knee as well as X & Y). I could have come up with a way to do both on the RF-45, but didn't put in the time. In practice, I have found that power feed on the Y is mostly useful for squaring up ends of stock.
I have yet to reposition the ram on my 935 - unless you're boring out motor blocks or the like I don't see the value in it. I have found it much simpler to angle the material being drilled than to take the head out of tram and have to re-align it later.
Keep in mind the extra cost items. I spent alsmost as much on the VFD controls + 3 power feeders + 4-axis DRO + Power Drawbar as I did on the mill.
Putting a Power drawbar on the 833 would take some effort but is totally doable. I would make a mounting plate that attached to the two cap screws holding the motor, and mount the PDB on that:
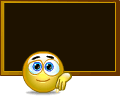
Power feed on the Y and powered head positioning are what drove me to the 935 (I put power feed on the knee as well as X & Y). I could have come up with a way to do both on the RF-45, but didn't put in the time. In practice, I have found that power feed on the Y is mostly useful for squaring up ends of stock.
I have yet to reposition the ram on my 935 - unless you're boring out motor blocks or the like I don't see the value in it. I have found it much simpler to angle the material being drilled than to take the head out of tram and have to re-align it later.
Keep in mind the extra cost items. I spent alsmost as much on the VFD controls + 3 power feeders + 4-axis DRO + Power Drawbar as I did on the mill.
Putting a Power drawbar on the 833 would take some effort but is totally doable. I would make a mounting plate that attached to the two cap screws holding the motor, and mount the PDB on that: