- Joined
- Feb 7, 2013
- Messages
- 2,486
I have a standard 9x42 Step pulley Enco vertical mill that was purchased new. It has been in my
posession for about 20 years but have rarely used the power down feed feature. I decided to use it
to drill a 1/4 inch hole at the slowest down feed speed at maybe 250 rpm drill speed. It started drilling
fine but the engagement bar kicked out after getting started. I took the assembly all apart and
made an adjustment there. Now the overload clutch slips when trying to drill a 1/4 inch hole.
I see a compression spring that apparently exerts pressure to the clutch overload cogs and
advanced that a little bit but it already seems fairly compressed. That didn't help much. I don't
want to break something inside so am wondering if drilling a 1/4 inch hole in mild steel would
be asking too much for this machine. The material thickness was .375 of an inch.
Just from estimation, it would probably down feed a 1/8 inch bit, however I prefer to manually
feed small bits as it is good practice to clear the chips using the down feed handle. Is this
something to look into or leave the machine as is and use the power down feed for only boring
operations?
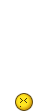
Edit: After a little research on the web, I found that the maximum drill size recommended for a standard Bridgeport type mill is 3/8 inch for power down feeding.....
posession for about 20 years but have rarely used the power down feed feature. I decided to use it
to drill a 1/4 inch hole at the slowest down feed speed at maybe 250 rpm drill speed. It started drilling
fine but the engagement bar kicked out after getting started. I took the assembly all apart and
made an adjustment there. Now the overload clutch slips when trying to drill a 1/4 inch hole.
I see a compression spring that apparently exerts pressure to the clutch overload cogs and
advanced that a little bit but it already seems fairly compressed. That didn't help much. I don't
want to break something inside so am wondering if drilling a 1/4 inch hole in mild steel would
be asking too much for this machine. The material thickness was .375 of an inch.
Just from estimation, it would probably down feed a 1/8 inch bit, however I prefer to manually
feed small bits as it is good practice to clear the chips using the down feed handle. Is this
something to look into or leave the machine as is and use the power down feed for only boring
operations?

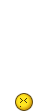
Edit: After a little research on the web, I found that the maximum drill size recommended for a standard Bridgeport type mill is 3/8 inch for power down feeding.....
Last edited: