- Joined
- Oct 14, 2014
- Messages
- 2,112
I bought my second 10EE a while back
After playing with the existing DC motor and drive, I gave up on repairing it. I did not try super hard, not too excited about maintaining an antique system. So all the old stuff got ripped out.
I have another thread where I got help with motor and VFD selection
www.hobby-machinist.com
My first 10EE lathe used a 5hp 3phase motor and VFD with a backgear. the machine has worked WONDERFULLY for 20 years now.
For this build I decided to go with a larger 10 Hp VFD rated motor to give low end torque without the need for a backgear. Simplifies the build quite a bit.
Here's pics of yesterday and today's work. had to get tricky to put the motor in place. made a "U" shaped fixture to hoist the motor so it could tuck inside the lathe cavity. the entire lathe is on a pallet truck to move left - right. the hoist is on a rail to move in - out.
yesterday, built a little fixture to hold a 5 turn potentiometer on the existing speed control knob. It is not quite assembled - I will replace the opaque plastic tube with a more flexible clear 1/4" plastic tube and clamp in place. This keeps the pot from being too rigidly attached and allow the operator to feel pot end of travel without breaking it. Soldering of wires will wait until all mechanical work is completed.
Machines Used | Monarch 10EE Toolroom Lathe with Taper Attachment and Chucks
Tool Post, Pneumatic Collet Closer and Installed Chuck NOT Included
www.machinesused.com
After playing with the existing DC motor and drive, I gave up on repairing it. I did not try super hard, not too excited about maintaining an antique system. So all the old stuff got ripped out.
I have another thread where I got help with motor and VFD selection
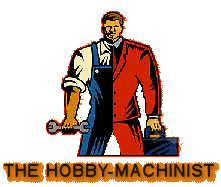
Which VFD for 10 hp spindle
I am seriously considering using this 10 hp 900 RPM motor to power the spindle on my 10EE https://www.ebay.com/itm/10-hp-electric-motor-284t-3-phase-900-rpm-severe-duty-PE284T-10-8C/184606676695 I have single phase only to run it. What would be a good VFD choice for this machine? NOT buying the...
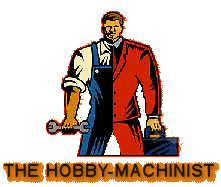
My first 10EE lathe used a 5hp 3phase motor and VFD with a backgear. the machine has worked WONDERFULLY for 20 years now.
For this build I decided to go with a larger 10 Hp VFD rated motor to give low end torque without the need for a backgear. Simplifies the build quite a bit.
Here's pics of yesterday and today's work. had to get tricky to put the motor in place. made a "U" shaped fixture to hoist the motor so it could tuck inside the lathe cavity. the entire lathe is on a pallet truck to move left - right. the hoist is on a rail to move in - out.
yesterday, built a little fixture to hold a 5 turn potentiometer on the existing speed control knob. It is not quite assembled - I will replace the opaque plastic tube with a more flexible clear 1/4" plastic tube and clamp in place. This keeps the pot from being too rigidly attached and allow the operator to feel pot end of travel without breaking it. Soldering of wires will wait until all mechanical work is completed.