- Joined
- Feb 1, 2015
- Messages
- 9,994
If you really want a challenge, my Grizzly G0602 Had a thread dial where the marks weren't concentric with the shaft so while some marks lined up exactly, others were off by a half a thread. A new dial cured the problem.
www.hobby-machinist.com
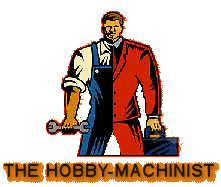
Threading On A Grizzly G0602
On March 19th, I replied to a thread begun by Cody Killgore entitled "Threading, Something Went Wrong Here" (post #19) where I show evidence of an problem with the threading dial on my Grizzly G0602. I had determined that the dial markings were not concentric with the gear shaft, creating an...
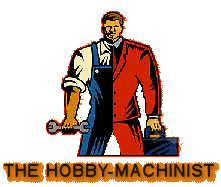