F
Firestopper
Forum Guest
Register Today
Thanks RE, it worked out and saves on floor space when not in use. I should prime both this and the die table tomorrow before 06:00 and let the sun bake it in. By 09:00 it should reach at least 103ºF. 
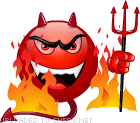
Turn and burn!
Paco

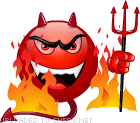
Turn and burn!
Paco