- Joined
- Feb 25, 2014
- Messages
- 349
About 5 years ago I decided that there was no perfect lathe for my shop. I had a SB13 that I spent 6 months restoring and it was a great lathe but I wanted more. I decided that I needed on big lathe and one small lathe to take the place of the SB13. Within 2 weeks I had bought 2 lathes and sold the SB.
This 14X54 Pacemaker is the big lathe I bought and it has been sitting un-touched on my shop floor for the last 5 years. Now I need to use it but before I can use it I need to do a little work to it. It was in pretty rough shape cosmetically and I never saw it under power but all the gears were in good shape and it was complete, so how bad could it be.
I started the tear down last week. I took off the compound, thread dial, taper attachment. micrometer stop, and anything else that was easy. Next up was the saddle and apron. I started by taking off the bearing carrier for the lead screw and feed rod and the end of the bed. There are spring loaded roller bearings in the carrier for the feed rod and the carrier has long dowel pins that locate it on the bed. I needed to run the carriage all the way to the head stock to have enough play in the feed rod and lead screw to permit the bearing carrier to come off the dowel pins (it took me a day to figure that out). The feed rod and lead screw are attached to the gear box output shafts with tapered pins and once they were driven out the feed rod and lead screw came out easily.
I wanted to separate the saddle and apron and remove them as 2 pieces but after a day of screwing around with separating them unsuccessfully I opted to take them off in one piece. I ran the carriage down to the end of the bed, loosened all the gibs and removed the whole assembly with the shop crane. There are 4 bolts and 1 large taper pin the hold the apron to the saddle, and then the apron is pulled forward and dropped down from the saddle. This whole procedure took me about 3 days.
Next I stripped off every instruction and label plate on the lathe and proceeded to clean, scrape, and strip paint of the entire machine. I'm 2 days into stripping paint and the end is nowhere in sight, I might have a full 2 weeks of stripping and sanding. I'm using Kleen Strip Aircraft paint stripper. I brush on a heavy coat and cover it with kitchen plastic wrap, let it sit for 90 minutes and then scrape it all off with a putty knife. The stripper takes everything off to bare metal (4 coats of paint and all the filler). This process is time critical, 60 minutes is too short and 120 minutes is too long.
Well that's where I'm at for now. Looks like tomorrow will be a snow day so I'll get a full day of stripping and scraping paint.
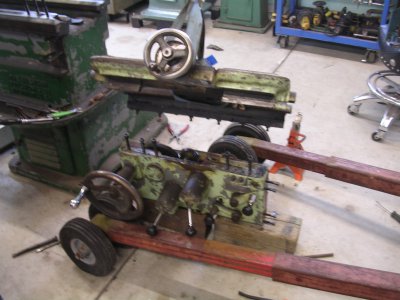
This 14X54 Pacemaker is the big lathe I bought and it has been sitting un-touched on my shop floor for the last 5 years. Now I need to use it but before I can use it I need to do a little work to it. It was in pretty rough shape cosmetically and I never saw it under power but all the gears were in good shape and it was complete, so how bad could it be.
I started the tear down last week. I took off the compound, thread dial, taper attachment. micrometer stop, and anything else that was easy. Next up was the saddle and apron. I started by taking off the bearing carrier for the lead screw and feed rod and the end of the bed. There are spring loaded roller bearings in the carrier for the feed rod and the carrier has long dowel pins that locate it on the bed. I needed to run the carriage all the way to the head stock to have enough play in the feed rod and lead screw to permit the bearing carrier to come off the dowel pins (it took me a day to figure that out). The feed rod and lead screw are attached to the gear box output shafts with tapered pins and once they were driven out the feed rod and lead screw came out easily.
I wanted to separate the saddle and apron and remove them as 2 pieces but after a day of screwing around with separating them unsuccessfully I opted to take them off in one piece. I ran the carriage down to the end of the bed, loosened all the gibs and removed the whole assembly with the shop crane. There are 4 bolts and 1 large taper pin the hold the apron to the saddle, and then the apron is pulled forward and dropped down from the saddle. This whole procedure took me about 3 days.
Next I stripped off every instruction and label plate on the lathe and proceeded to clean, scrape, and strip paint of the entire machine. I'm 2 days into stripping paint and the end is nowhere in sight, I might have a full 2 weeks of stripping and sanding. I'm using Kleen Strip Aircraft paint stripper. I brush on a heavy coat and cover it with kitchen plastic wrap, let it sit for 90 minutes and then scrape it all off with a putty knife. The stripper takes everything off to bare metal (4 coats of paint and all the filler). This process is time critical, 60 minutes is too short and 120 minutes is too long.
Well that's where I'm at for now. Looks like tomorrow will be a snow day so I'll get a full day of stripping and scraping paint.
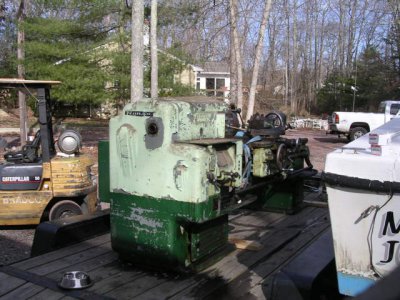
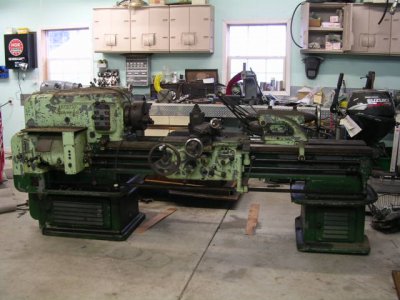
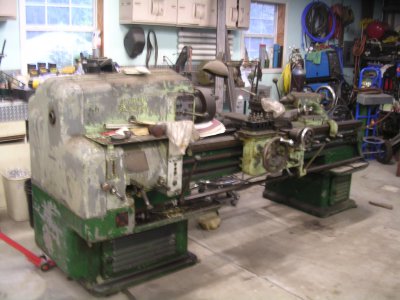
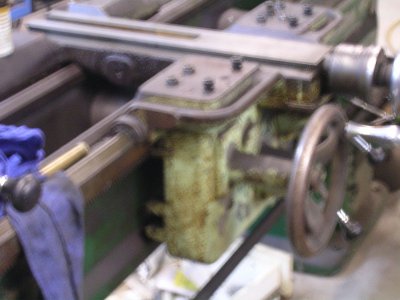
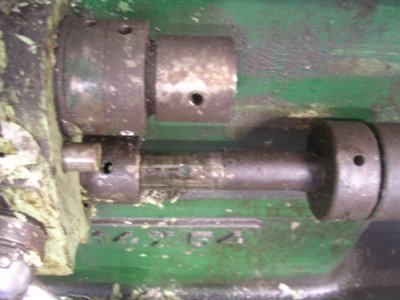
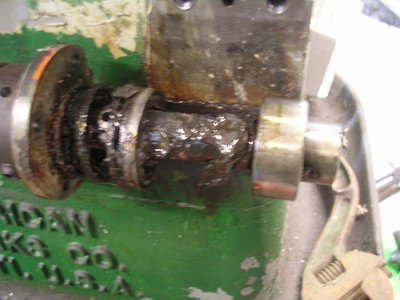
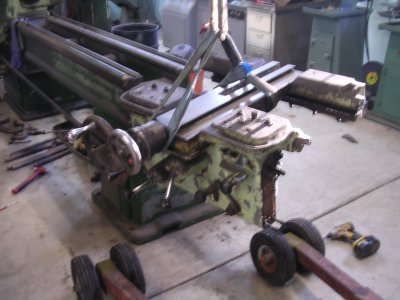
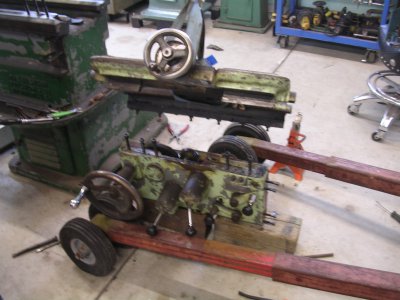