- Joined
- Jan 2, 2019
- Messages
- 6,568
Thanks, I already have the motor and it worked fine except for the stock mounting.
It’s a CNC project so eventually want to control the spindle in software. If it turns out not great I’ve got less than $100 into it and would be looking for another small servo.
Here’s that project.
www.hobby-machinist.com
John
It’s a CNC project so eventually want to control the spindle in software. If it turns out not great I’ve got less than $100 into it and would be looking for another small servo.
Here’s that project.
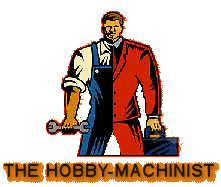
Homemade vertical mill drill
Well, I guess I'm gonna try to make myself a mill for cheap. I found this column on Craigslist for $80. And I ordered this spindle I can power with a VFD I already have. And I'm going to get one of these cheap x-y milling tables. And probably look for a really flat piece of C channel...
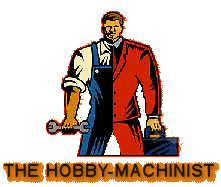
John