- Joined
- Dec 7, 2011
- Messages
- 61
In 2007 I inherited a Southbend 9" Model C lathe from my uncle in Durban, South Africa. On receiving the machine at my home workshop in Walvis Bay, Namibia, I immediately set about restoring the lathe. I knew that I would be into this project for a while, but never realised that I would tax all of my experience as a marine engineer, to the limits.
HISTORY: The serial number of this lathe is 37193 NCR9. From Tony Griffiths site I discovered that this SB lathe was manufactured in 1927. This lathe was originally purchased by the Durban technical training centre (now called the Technicon) to teach apprentices how to use a lathe and was bought by my uncle at an auction, after the second world war, in who's care this machine was until it followed me home. Here are some before pictures;
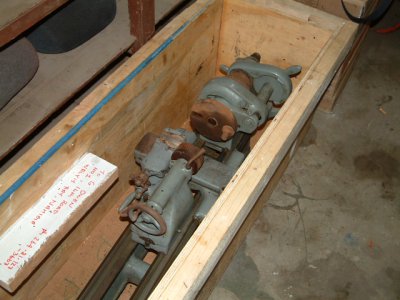


INITIAL REBUILD: I first unpacked the machine and lay all of the parts on my workshop floor. Over the time span of four weekends I progressivly stripped and cleaned all major component parts of the lathe and re-assembled them, leaving the lathe in it's major components, as I realised that some work was required on the lathe bed and mating slides. These photos show some cleaned and overhauled components;


SCRAPING THE WAYS AND SLIDES: This is where the fun started. It took 6 months at two hours per day to re-scrape the bed and the slide ways. Little did I know how long it would take me to do. It was the first time that I had attempted to do this on a lathe. I've scraped in many white metal main, bottom end and cross-head bearings on low speed marine diesel engines, but cast iron, I learn't, was a different story. White metal is much softer than cast iron and your hands really take a beating from holding the hand scrapers over a period of time. Here are the photos of the lathe bed and slides, during the hand scraping process, showing my tools used to hand scrape the ways;


Here are some close up photos of the tailstock and saddle slide bearing surfaces during the hand scraping operation;


Here are some photos of the finished tailstock and saddle slide bearing surfaces after hand scraping;

This post will be continued.

HISTORY: The serial number of this lathe is 37193 NCR9. From Tony Griffiths site I discovered that this SB lathe was manufactured in 1927. This lathe was originally purchased by the Durban technical training centre (now called the Technicon) to teach apprentices how to use a lathe and was bought by my uncle at an auction, after the second world war, in who's care this machine was until it followed me home. Here are some before pictures;
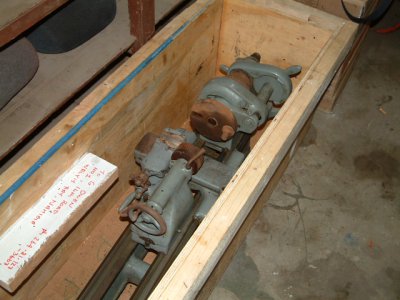


INITIAL REBUILD: I first unpacked the machine and lay all of the parts on my workshop floor. Over the time span of four weekends I progressivly stripped and cleaned all major component parts of the lathe and re-assembled them, leaving the lathe in it's major components, as I realised that some work was required on the lathe bed and mating slides. These photos show some cleaned and overhauled components;


SCRAPING THE WAYS AND SLIDES: This is where the fun started. It took 6 months at two hours per day to re-scrape the bed and the slide ways. Little did I know how long it would take me to do. It was the first time that I had attempted to do this on a lathe. I've scraped in many white metal main, bottom end and cross-head bearings on low speed marine diesel engines, but cast iron, I learn't, was a different story. White metal is much softer than cast iron and your hands really take a beating from holding the hand scrapers over a period of time. Here are the photos of the lathe bed and slides, during the hand scraping process, showing my tools used to hand scrape the ways;


Here are some close up photos of the tailstock and saddle slide bearing surfaces during the hand scraping operation;


Here are some photos of the finished tailstock and saddle slide bearing surfaces after hand scraping;

This post will be continued.
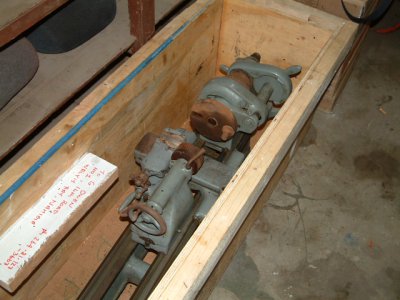









