Recently I acquired a new (to me) saddle and table for my Burke #4 mill. It has made such a great improvement over the "FrankenBurke" setup I had, But has led me to some things that need additional attention.
The first thing was , my old converted table had a 7/16" slot , the new table has a 1/2" slot. The 7/16" hold down set works fine but the T nuts are a little sloppy, so I made some new ones. I took a .900" x .500" bar and milled a step on each side , the sawed it into .875" lengths and drilled and tapped it for 3/8-16.
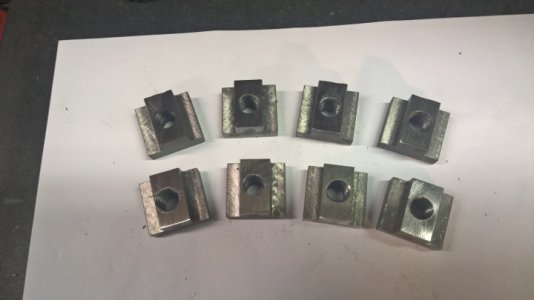
These are the finished T nuts and they fit the Burke table perfectly. I stopped the tap early so the last thread in the hole is not complete and the studs will stop instead of screwing through and hitting the table. ( a little extra work , but worth the effort).
The next item on my list for this machine is the vertical head was shop adapted with a long shaft and bar to be used in the top overarm hole in the machine. While this gave more room between the table and head, it required a separate drive or the use of the backwoods hillbilly setup they came up with to drive it from the spindle with pulleys on the back (which worked poorly at best). I wanted to take it back to the factory mounting but the parts are about... no are impossible to find. I need three parts and decided to make them.
First up is a new shaft for the vertical head. I have the drawing for the factory shaft , but decided to leave off the B&S 9 taper and have a 3/4" stub to go in a collet. This will make it smaller and easier to leave on the machine and just swing up when not in use. I got a piece of 1 1/4" CRS bar stock to turn the 1.125" shaft. I have never had the need to turn between centers till now. this was the only way to make this on my lathe due to length. I also did not have a large enough lathe dog for this ....soooooo I fabricated one that worked nicely.
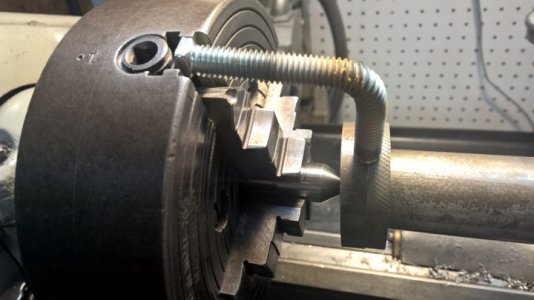
This is my home made lathe dog. a steel ring and a bent carriage bolt with a set screw in the bottom.
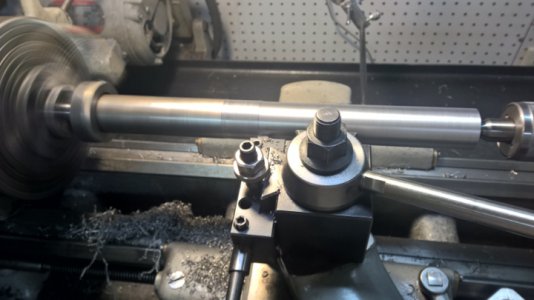
Here , turning the shaft between centers.
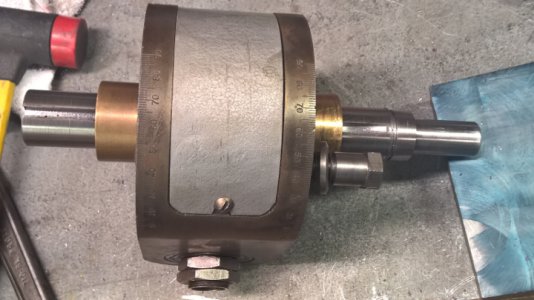
After milling a key way the length of the shaft, it fits perfectly. I made the shaft three inches longer than the factory shaft so the head can be moved out farther on the overarm for more versatility.
Next item needed is an easy one to make. The eccentric busing for the mounting plate. I turned a piece of 3" diameter CRS to 2.250" diameter leaving a .250 flange the 3"diam. and then bored a 2" hole through it .050" off center.
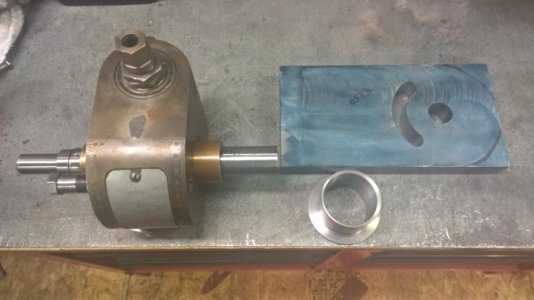
Of course , the last piece is the mounting plate. Burke used cast iron , but a chunk of cast iron this size came with a $100 price tag. I decided a $15 piece of 1" thick steel bar stock was a better idea. In the photo, you can see the new shaft in the head, the eccentric bushing ( I will slit the one side before installing) and the mounting plate , so far. I have milled the 90 degree slot for the head to be able to tilt and started the fist hole. As soon as I bore the holes and make the pinch bolt, I will have the machine back to like factory . I Hope to finish this up in the next couple days.
After this is done, I have a D.C. motor and controller to run the power feed with instead of pulleys and belts off the spindle. It will give me infinite settings for feed rates.
The first thing was , my old converted table had a 7/16" slot , the new table has a 1/2" slot. The 7/16" hold down set works fine but the T nuts are a little sloppy, so I made some new ones. I took a .900" x .500" bar and milled a step on each side , the sawed it into .875" lengths and drilled and tapped it for 3/8-16.
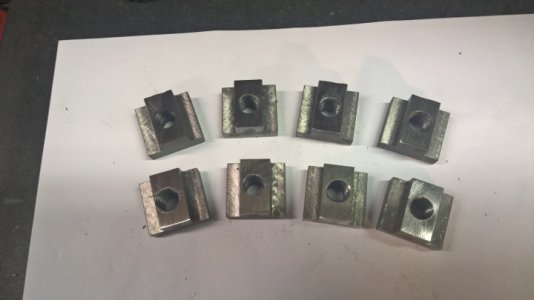
These are the finished T nuts and they fit the Burke table perfectly. I stopped the tap early so the last thread in the hole is not complete and the studs will stop instead of screwing through and hitting the table. ( a little extra work , but worth the effort).
The next item on my list for this machine is the vertical head was shop adapted with a long shaft and bar to be used in the top overarm hole in the machine. While this gave more room between the table and head, it required a separate drive or the use of the backwoods hillbilly setup they came up with to drive it from the spindle with pulleys on the back (which worked poorly at best). I wanted to take it back to the factory mounting but the parts are about... no are impossible to find. I need three parts and decided to make them.
First up is a new shaft for the vertical head. I have the drawing for the factory shaft , but decided to leave off the B&S 9 taper and have a 3/4" stub to go in a collet. This will make it smaller and easier to leave on the machine and just swing up when not in use. I got a piece of 1 1/4" CRS bar stock to turn the 1.125" shaft. I have never had the need to turn between centers till now. this was the only way to make this on my lathe due to length. I also did not have a large enough lathe dog for this ....soooooo I fabricated one that worked nicely.
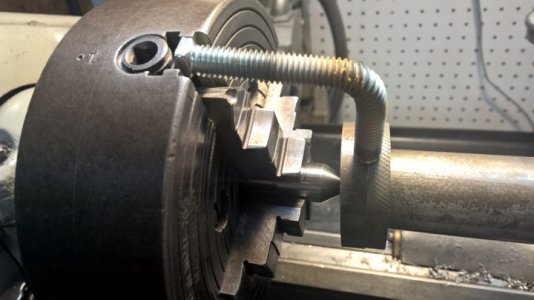
This is my home made lathe dog. a steel ring and a bent carriage bolt with a set screw in the bottom.
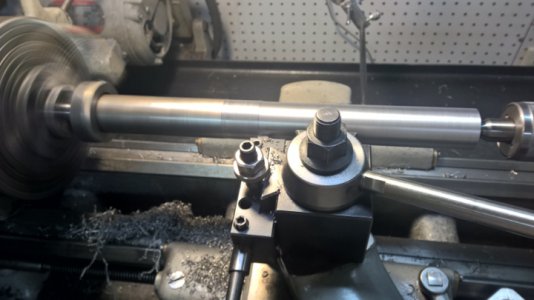
Here , turning the shaft between centers.
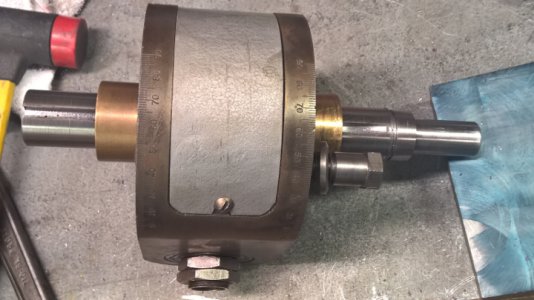
After milling a key way the length of the shaft, it fits perfectly. I made the shaft three inches longer than the factory shaft so the head can be moved out farther on the overarm for more versatility.
Next item needed is an easy one to make. The eccentric busing for the mounting plate. I turned a piece of 3" diameter CRS to 2.250" diameter leaving a .250 flange the 3"diam. and then bored a 2" hole through it .050" off center.
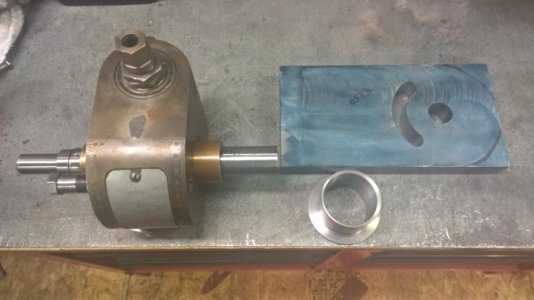
Of course , the last piece is the mounting plate. Burke used cast iron , but a chunk of cast iron this size came with a $100 price tag. I decided a $15 piece of 1" thick steel bar stock was a better idea. In the photo, you can see the new shaft in the head, the eccentric bushing ( I will slit the one side before installing) and the mounting plate , so far. I have milled the 90 degree slot for the head to be able to tilt and started the fist hole. As soon as I bore the holes and make the pinch bolt, I will have the machine back to like factory . I Hope to finish this up in the next couple days.
After this is done, I have a D.C. motor and controller to run the power feed with instead of pulleys and belts off the spindle. It will give me infinite settings for feed rates.