Hello all,
I would like to share my CNC conversion with this site. Over the last 1.5yrs i've been looking at all the different conversion done with Grizzly and Precision Matthews bench top mills. I choose this site to share the build because I enjoy the atmosphere and all types of projects shared by its members.
This mill wasn't my first choice for a bench top conversion, but I got a great deal on it.....free. Well not entirely free, i had to barter my time in exchange for it. I've acquired alot of parts over the last year and even made a few parts at my local Makerspace for the conversion. Now I plan on tackling a major upgrade...changes to the a column. I won't provide too many details at this point because well...its going to take alot of work to make it right and i'm still thinking through the steps on how to make it. Here is a few pictures of what i'm planning.
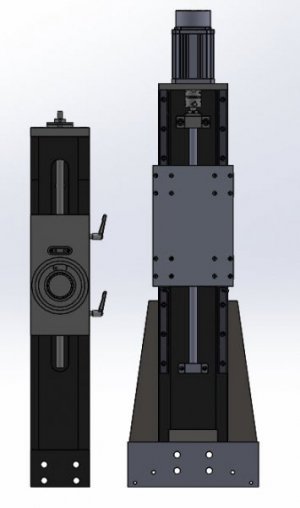
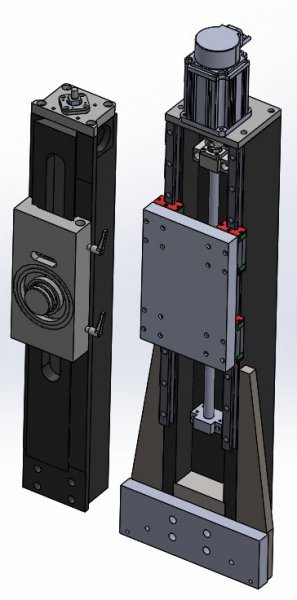
You can see the size difference between with the G0704 column assembly and the one i'm planning on doing . I know doing these upgrades doesn't make sense but who cares
. Hopefully I can learn a lot on machining. I've spent way too many hours in front of a computer designing stuff so now its time for me to start making them. I was able to pick up the material today and hopefully soon I will make start machining
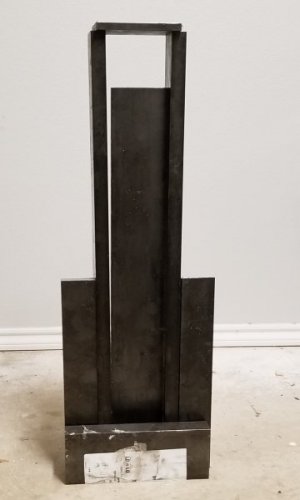
Progress and updates will be a bit slow because I can only spend a few hours a week machining parts and its about a 40 mile drive to the local makerspace in Dallas
Thanks and I hope you all enjoy the build
V
I would like to share my CNC conversion with this site. Over the last 1.5yrs i've been looking at all the different conversion done with Grizzly and Precision Matthews bench top mills. I choose this site to share the build because I enjoy the atmosphere and all types of projects shared by its members.
This mill wasn't my first choice for a bench top conversion, but I got a great deal on it.....free. Well not entirely free, i had to barter my time in exchange for it. I've acquired alot of parts over the last year and even made a few parts at my local Makerspace for the conversion. Now I plan on tackling a major upgrade...changes to the a column. I won't provide too many details at this point because well...its going to take alot of work to make it right and i'm still thinking through the steps on how to make it. Here is a few pictures of what i'm planning.
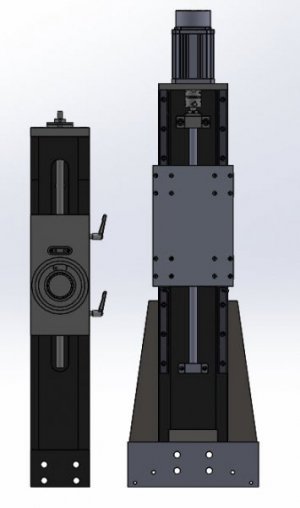
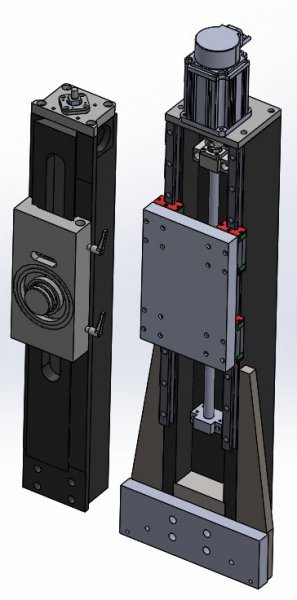
You can see the size difference between with the G0704 column assembly and the one i'm planning on doing . I know doing these upgrades doesn't make sense but who cares
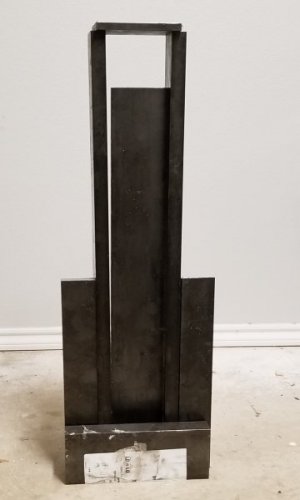
Progress and updates will be a bit slow because I can only spend a few hours a week machining parts and its about a 40 mile drive to the local makerspace in Dallas
Thanks and I hope you all enjoy the build
V