- Joined
- Feb 1, 2015
- Messages
- 9,939
I recently took a critical look at my Grizzly 6 -1/2" 4 jaw chuck and found the jaw grind to be seriously deficient and I decided to try to regrind my jaws.
I have a Craftsman 1/4" die grinder that I would press into service but I needed to come up with a stable mount for the grinder. My design utilized the AXA style QCTP and a Shars 5/8" tool holder. This design permitted me to adjust the angle of the die grinder spindle axis to the lathe spindle axis as well as the height of the die grinder relative to the lathe spindle axis
In order to grind the jaws of a lathe chuck in situ, some means of preloading the jaws mimicking conditions of use is required. For 2 piece jaws, a ring which utilizes one of the jaw mounting screws can be used but some other method must be used for single piece jaws. My approach was to use the 45º bevels on the jaws so that the side force is balanced by the adjacent jaws.
I made the preload plate from a piece of 1/4" HR steel. The cutout was machined on my Tormach although it could have been made on a manual mill with a RT. A 1/4" carbide EM was used. The 135º inside corner sharp was finished with a small file. The OD was roughed out on the4 band saw and turned on the lathe.
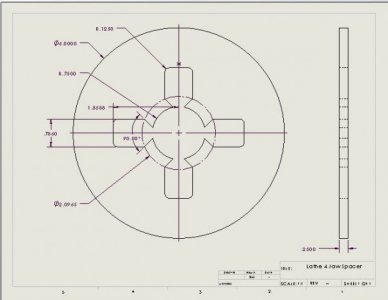
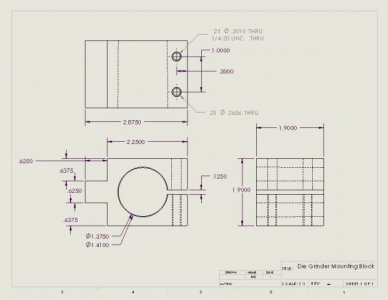
The die grinder mount was made from a 2 x 2 x3" block of HR steel. The exterior was milled first and pilot hole followed by a 1/2" drill. The block was then mounted in the 4 jaw and a 1/2" pin was inserted in the hole for the purpose of centering the hole in the block to the lathe axis.
The hole was drilled out to 7/8" and then bored to 1.375". The Craftsman die grinder has a tapered nose so the compound was rotated to match the taper of .0175"/1.90" and the final cut was made using the compound feed.
The mount was then transferred to the mill where the holes for the clamping screws were drilled and tapped and slot for the clamp was cut with an 1/8" end mill. Because the EM wasn't long enough to cut the full slot, I finished cutting through with the band saw and cleaned the slot with a flat file.
The faces of the chuck jaws were blued so the grinding progress could be monitored. The preload plate was mounted on the chuck and the jaws were lightly snugged up. The jaws were then gradually tightened to ensure a balanced load on each jaw. A fairly heavy load was used.
A 3/4" cylindrical point was used for grinding. The grinder was centered vertically and adjusted so its axis was parallel to the lathe axis. The lathe was set for the lowest speed (150 rpm) and the feed was set at .007"/rev.
Before commenting on the lack of protection for the ways, the photo was set up after the fact. Way protection was used.
The grinder and the lathe were turned on and the grinder move out to just engage the chuck jaw. It was then fed in to a point where the far end of the grinding point was about 1/2" past the inside face of the jaw. The feed was then reversed to bring the grinding point clear of the jaw. The grinder was then moved out by .0015" and the process repeated.
One jaw extended considerably more than the other three so quite a few passes were required before the other three jaws were engaged.
The taper of the original grind was about .007" over length of the jaw. In addition, the original grind had a radius of curvature of about 1.1" whereas the maximum radius that I could grind in situ is about .75". Because of this, I had to grind an additional .004" to carry the grind to the edge of the jaw face. All in all, I had to remove about .011" after intial contact was made with the last jaw.
After grinding, the jaws were checked for taper. With a moderate load on the jaws, the diameter at the rear of the jaws was .0015 larger than the front. A 1"inch bar was mounted in the chuck and adjusted for zero runout. The indicator was moved to a distance 9" from the chuck and the bar was checked for stability. Whereas with the original grind, the bar could be set at any position within a .014" radius, now when the bar was deflected it returned to its original position within .0001"
Success!
While I don't anticipate having to regrind the jaws, I numbered the jaws so they can be inserted in the same position each time and I also indexed the spacer so I can load it in the same position as the first grind.

I have a Craftsman 1/4" die grinder that I would press into service but I needed to come up with a stable mount for the grinder. My design utilized the AXA style QCTP and a Shars 5/8" tool holder. This design permitted me to adjust the angle of the die grinder spindle axis to the lathe spindle axis as well as the height of the die grinder relative to the lathe spindle axis
In order to grind the jaws of a lathe chuck in situ, some means of preloading the jaws mimicking conditions of use is required. For 2 piece jaws, a ring which utilizes one of the jaw mounting screws can be used but some other method must be used for single piece jaws. My approach was to use the 45º bevels on the jaws so that the side force is balanced by the adjacent jaws.
I made the preload plate from a piece of 1/4" HR steel. The cutout was machined on my Tormach although it could have been made on a manual mill with a RT. A 1/4" carbide EM was used. The 135º inside corner sharp was finished with a small file. The OD was roughed out on the4 band saw and turned on the lathe.
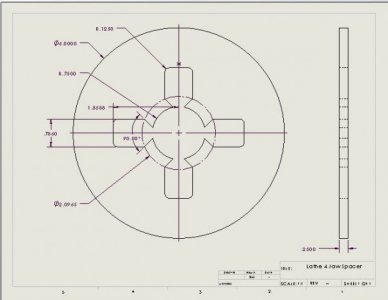
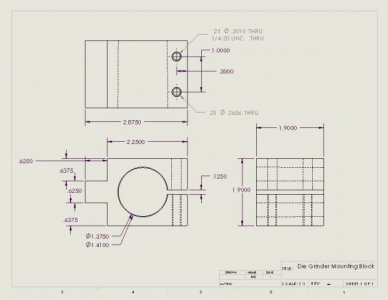
The die grinder mount was made from a 2 x 2 x3" block of HR steel. The exterior was milled first and pilot hole followed by a 1/2" drill. The block was then mounted in the 4 jaw and a 1/2" pin was inserted in the hole for the purpose of centering the hole in the block to the lathe axis.
The hole was drilled out to 7/8" and then bored to 1.375". The Craftsman die grinder has a tapered nose so the compound was rotated to match the taper of .0175"/1.90" and the final cut was made using the compound feed.
The mount was then transferred to the mill where the holes for the clamping screws were drilled and tapped and slot for the clamp was cut with an 1/8" end mill. Because the EM wasn't long enough to cut the full slot, I finished cutting through with the band saw and cleaned the slot with a flat file.
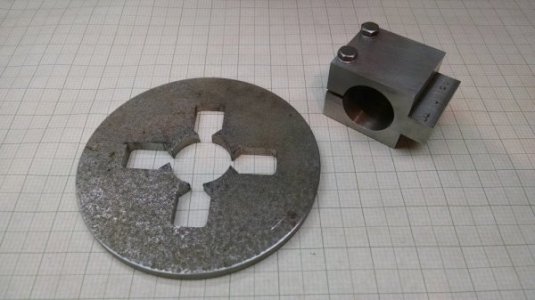
The faces of the chuck jaws were blued so the grinding progress could be monitored. The preload plate was mounted on the chuck and the jaws were lightly snugged up. The jaws were then gradually tightened to ensure a balanced load on each jaw. A fairly heavy load was used.
A 3/4" cylindrical point was used for grinding. The grinder was centered vertically and adjusted so its axis was parallel to the lathe axis. The lathe was set for the lowest speed (150 rpm) and the feed was set at .007"/rev.
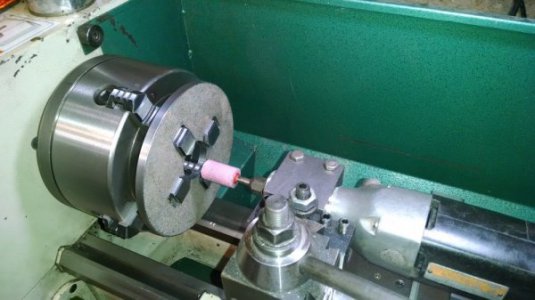

Before commenting on the lack of protection for the ways, the photo was set up after the fact. Way protection was used.
The grinder and the lathe were turned on and the grinder move out to just engage the chuck jaw. It was then fed in to a point where the far end of the grinding point was about 1/2" past the inside face of the jaw. The feed was then reversed to bring the grinding point clear of the jaw. The grinder was then moved out by .0015" and the process repeated.
One jaw extended considerably more than the other three so quite a few passes were required before the other three jaws were engaged.
The taper of the original grind was about .007" over length of the jaw. In addition, the original grind had a radius of curvature of about 1.1" whereas the maximum radius that I could grind in situ is about .75". Because of this, I had to grind an additional .004" to carry the grind to the edge of the jaw face. All in all, I had to remove about .011" after intial contact was made with the last jaw.
After grinding, the jaws were checked for taper. With a moderate load on the jaws, the diameter at the rear of the jaws was .0015 larger than the front. A 1"inch bar was mounted in the chuck and adjusted for zero runout. The indicator was moved to a distance 9" from the chuck and the bar was checked for stability. Whereas with the original grind, the bar could be set at any position within a .014" radius, now when the bar was deflected it returned to its original position within .0001"
Success!
While I don't anticipate having to regrind the jaws, I numbered the jaws so they can be inserted in the same position each time and I also indexed the spacer so I can load it in the same position as the first grind.
